નબળું પાણી પ્રતિકાર, અસમાન સપાટી, ઉચ્ચ પાવડર સામગ્રી અને અસમાન લંબાઈ? જળચર ખોરાક ઉત્પાદનમાં સામાન્ય સમસ્યાઓ અને સુધારાના પગલાં
જળચર ખોરાકના અમારા દૈનિક ઉત્પાદનમાં, અમને વિવિધ પાસાઓથી કેટલીક સમસ્યાઓનો સામનો કરવો પડ્યો છે. અહીં કેટલાક ઉદાહરણો છે જેની ચર્ચા દરેક સાથે નીચે મુજબ છે:
૧, ફોર્મ્યુલા
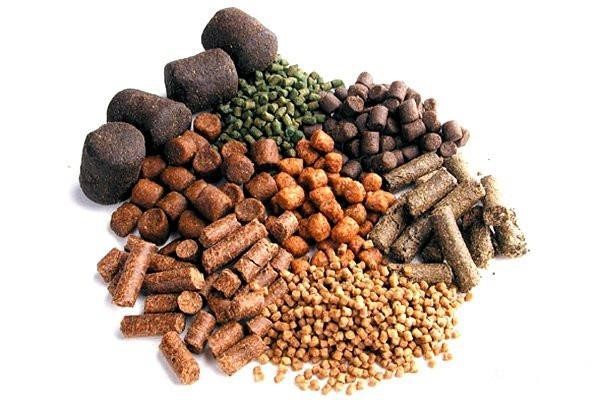
1. માછલીના ખોરાકના ફોર્મ્યુલા માળખામાં, વધુ પ્રકારના મીલ કાચા માલ હોય છે, જેમ કે રેપસીડ મીલ, કોટન મીલ, વગેરે, જે ક્રૂડ ફાઇબરથી સંબંધિત હોય છે. કેટલીક તેલ ફેક્ટરીઓમાં અદ્યતન ટેકનોલોજી હોય છે, અને તેલ મૂળભૂત રીતે ખૂબ ઓછી સામગ્રી સાથે સૂકવીને તળવામાં આવે છે. વધુમાં, આ પ્રકારના કાચા માલ ઉત્પાદનમાં સરળતાથી શોષી શકાતા નથી, જેની દાણાદારી પર ઘણી અસર પડે છે. વધુમાં, કપાસ મીલને કચડી નાખવું મુશ્કેલ છે, જે કાર્યક્ષમતાને અસર કરે છે.
2. ઉકેલ: રેપસીડ કેકનો ઉપયોગ વધ્યો છે, અને ઉચ્ચ-ગુણવત્તાવાળા સ્થાનિક ઘટકો જેમ કે ચોખાના ભૂસાને ફોર્મ્યુલામાં ઉમેરવામાં આવ્યા છે. વધુમાં, ઘઉં, જે ફોર્મ્યુલામાં આશરે 5-8% હિસ્સો ધરાવે છે, તે ઉમેરવામાં આવ્યું છે. ગોઠવણ દ્વારા, 2009 માં દાણાદાર અસર પ્રમાણમાં આદર્શ છે, અને પ્રતિ ટન ઉપજ પણ વધ્યો છે. 2.5 મીમી કણો 8-9 ટન વચ્ચે છે, જે ભૂતકાળની તુલનામાં લગભગ 2 ટનનો વધારો છે. કણોના દેખાવમાં પણ નોંધપાત્ર સુધારો થયો છે.
વધુમાં, કપાસિયા ખોળને ક્રશ કરવાની કાર્યક્ષમતા સુધારવા માટે, અમે ક્રશ કરતા પહેલા કપાસિયા ખોળ અને રેપસીડ ખોળને 2:1 ના ગુણોત્તરમાં મિશ્રિત કર્યા. સુધારણા પછી, ક્રશિંગ ગતિ મૂળભૂત રીતે રેપસીડ ખોળના ક્રશિંગ ગતિ જેટલી જ હતી.
૨, કણોની અસમાન સપાટી
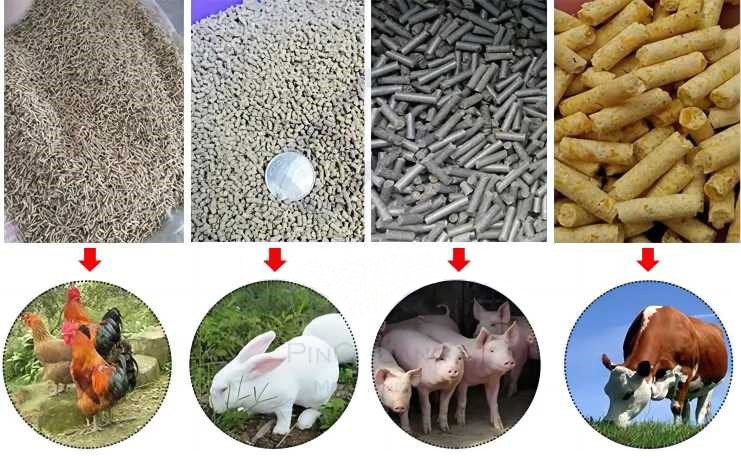
૧. તૈયાર ઉત્પાદનના દેખાવ પર તેની મોટી અસર પડે છે, અને જ્યારે પાણીમાં ઉમેરવામાં આવે છે, ત્યારે તે તૂટી જવાની સંભાવના ધરાવે છે અને તેનો ઉપયોગ દર ઓછો હોય છે. મુખ્ય કારણ છે:
(1) કાચા માલને ખૂબ જ બરછટ કચડી નાખવામાં આવે છે, અને ટેમ્પરિંગ પ્રક્રિયા દરમિયાન, તે સંપૂર્ણપણે પરિપક્વ અને નરમ થતા નથી, અને ઘાટના છિદ્રોમાંથી પસાર થતી વખતે તેને અન્ય કાચા માલ સાથે સારી રીતે જોડી શકાતા નથી.
(૨) કાચા ફાઇબરની ઉચ્ચ સામગ્રી ધરાવતા ફિશ ફીડ ફોર્મ્યુલામાં, ટેમ્પરિંગ પ્રક્રિયા દરમિયાન કાચા માલમાં વરાળ પરપોટાની હાજરીને કારણે, કણ સંકોચન દરમિયાન ઘાટની અંદર અને બહાર દબાણના તફાવતને કારણે આ પરપોટા ફાટી જાય છે, જેના પરિણામે કણોની સપાટી અસમાન બને છે.
2. સંભાળવાના પગલાં:
(૧) ક્રશિંગ પ્રક્રિયાને યોગ્ય રીતે નિયંત્રિત કરો
હાલમાં, માછલીના ખોરાકનું ઉત્પાદન કરતી વખતે, અમારી કંપની જથ્થાબંધ કાચા માલ તરીકે 1.2 મીમી ચાળણીના સૂક્ષ્મ પાવડરનો ઉપયોગ કરે છે. ક્રશિંગની સૂક્ષ્મતા સુનિશ્ચિત કરવા માટે અમે ચાળણીના ઉપયોગની આવર્તન અને હથોડાના ઘસારાની ડિગ્રીને નિયંત્રિત કરીએ છીએ.
(2) વરાળ દબાણ નિયંત્રિત કરો
સૂત્ર અનુસાર, ઉત્પાદન દરમિયાન વરાળના દબાણને વાજબી રીતે સમાયોજિત કરો, સામાન્ય રીતે 0.2 ની આસપાસ નિયંત્રિત કરો. માછલીના ખોરાકના સૂત્રમાં મોટા પ્રમાણમાં બરછટ ફાઇબર કાચા માલ હોવાને કારણે, ઉચ્ચ-ગુણવત્તાવાળી વરાળ અને વાજબી ટેમ્પરિંગ સમય જરૂરી છે.
૩, કણોનો નબળો પાણી પ્રતિકાર
૧. આ પ્રકારની સમસ્યા આપણા રોજિંદા ઉત્પાદનમાં સૌથી સામાન્ય છે, જે સામાન્ય રીતે નીચેના પરિબળો સાથે સંબંધિત છે:
(૧) ટૂંકા ટેમ્પરિંગ સમય અને ઓછા ટેમ્પરિંગ તાપમાનના પરિણામે અસમાન અથવા અપૂરતું ટેમ્પરિંગ, ઓછી પાકવાની ડિગ્રી અને અપૂરતી ભેજ થાય છે.
(2) સ્ટાર્ચ જેવા અપૂરતા એડહેસિવ પદાર્થો.
(3) રિંગ મોલ્ડનો કમ્પ્રેશન રેશિયો ખૂબ ઓછો છે.
(૪) ફોર્મ્યુલામાં તેલનું પ્રમાણ અને ક્રૂડ ફાઇબર કાચા માલનું પ્રમાણ ખૂબ વધારે છે.
(5) કણ કદ પરિબળને કચડી નાખવું.
2. સંભાળવાના પગલાં:
(1) વરાળની ગુણવત્તામાં સુધારો કરો, રેગ્યુલેટરના બ્લેડ એંગલને સમાયોજિત કરો, ટેમ્પરિંગ સમય લંબાવો અને કાચા માલના ભેજનું પ્રમાણ યોગ્ય રીતે વધારશો.
(2) ફોર્મ્યુલાને સમાયોજિત કરો, સ્ટાર્ચ કાચા માલનું પ્રમાણ યોગ્ય રીતે વધારો, અને ચરબી અને કાચા ફાઇબર કાચા માલનું પ્રમાણ ઘટાડવું.
(૩) જો જરૂરી હોય તો એડહેસિવ ઉમેરો. (સોડિયમ આધારિત બેન્ટોનાઇટ સ્લરી)
(૪) ના સંકોચન ગુણોત્તરમાં સુધારોરિંગ ડાઇ
(૫) કૂવામાં ભૂકો કરવાની સૂક્ષ્મતા નિયંત્રિત કરો
૪, કણોમાં વધુ પડતું પાવડરનું પ્રમાણ
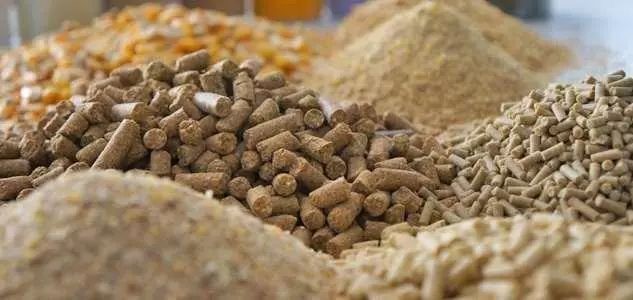
૧. ઠંડુ થયા પછી અને સ્ક્રીનીંગ પહેલાં સામાન્ય પેલેટ ફીડનો દેખાવ સુનિશ્ચિત કરવો મુશ્કેલ છે. ગ્રાહકોએ અહેવાલ આપ્યો છે કે ગોળીઓમાં વધુ બારીક રાખ અને પાવડર હોય છે. ઉપરોક્ત વિશ્લેષણના આધારે, મને લાગે છે કે આના ઘણા કારણો છે:
A. કણોની સપાટી સુંવાળી નથી, ચીરો સુઘડ નથી, અને કણો છૂટા છે અને પાવડર ઉત્પાદન માટે સંવેદનશીલ છે;
B. સ્ક્રીનને ગ્રેડ કરીને અધૂરી સ્ક્રીનીંગ, ભરાયેલી સ્ક્રીન મેશ, રબરના બોલનો ગંભીર ઘસારો, મેળ ન ખાતી સ્ક્રીન મેશ છિદ્ર, વગેરે;
C. ફિનિશ્ડ પ્રોડક્ટ વેરહાઉસમાં ઘણી બધી ઝીણી રાખના અવશેષો છે, અને ક્લિયરન્સ સંપૂર્ણ નથી;
D. પેકેજિંગ અને વજન કરતી વખતે ધૂળ દૂર કરવામાં છુપાયેલા જોખમો છે;
સંભાળવાના પગલાં:
A. ફોર્મ્યુલા સ્ટ્રક્ચરને ઑપ્ટિમાઇઝ કરો, રિંગ ડાઇને યોગ્ય રીતે પસંદ કરો અને કમ્પ્રેશન રેશિયોને સારી રીતે નિયંત્રિત કરો.
B. ગ્રાન્યુલેશન પ્રક્રિયા દરમિયાન, કાચા માલને સંપૂર્ણપણે પાકવા અને નરમ કરવા માટે ટેમ્પરિંગ સમય, ખોરાક આપવાની માત્રા અને ગ્રાન્યુલેશન તાપમાનને નિયંત્રિત કરો.
C. ખાતરી કરો કે કણોનો ક્રોસ-સેક્શન સુઘડ છે અને સ્ટીલની પટ્ટીથી બનેલા નરમ કાપવાના છરીનો ઉપયોગ કરો.
D. ગ્રેડિંગ સ્ક્રીનને સમાયોજિત કરો અને જાળવો, અને વાજબી સ્ક્રીન ગોઠવણીનો ઉપયોગ કરો.
E. ફિનિશ્ડ પ્રોડક્ટ વેરહાઉસ હેઠળ સેકન્ડરી સ્ક્રીનીંગ ટેકનોલોજીનો ઉપયોગ પાવડર સામગ્રીના ગુણોત્તરને ઘણો ઘટાડી શકે છે.
F. ફિનિશ્ડ પ્રોડક્ટ વેરહાઉસ અને સર્કિટને સમયસર સાફ કરવું જરૂરી છે. વધુમાં, પેકેજિંગ અને ધૂળ દૂર કરવાના ઉપકરણમાં સુધારો કરવો જરૂરી છે. ધૂળ દૂર કરવા માટે નકારાત્મક દબાણનો ઉપયોગ કરવો શ્રેષ્ઠ છે, જે વધુ આદર્શ છે. ખાસ કરીને પેકેજિંગ પ્રક્રિયા દરમિયાન, પેકેજિંગ કાર્યકર નિયમિતપણે પેકેજિંગ સ્કેલના બફર હોપરમાંથી ધૂળને પછાડીને સાફ કરે છે..
૫, કણોની લંબાઈ બદલાય છે
1. દૈનિક ઉત્પાદનમાં, અમને ઘણીવાર નિયંત્રણમાં મુશ્કેલીઓનો સામનો કરવો પડે છે, ખાસ કરીને 420 થી ઉપરના મોડેલો માટે. આના કારણોનો સારાંશ નીચે મુજબ છે:
(1) દાણાદાર માટે ખોરાક આપવાની માત્રા અસમાન છે, અને ટેમ્પરિંગ અસરમાં મોટા પ્રમાણમાં વધઘટ થાય છે.
(2) મોલ્ડ રોલર્સ વચ્ચે અસંગત અંતર અથવા રિંગ મોલ્ડ અને પ્રેશર રોલર્સનો ગંભીર ઘસારો.
(૩) રિંગ મોલ્ડની અક્ષીય દિશામાં, બંને છેડા પર ડિસ્ચાર્જ ગતિ મધ્યમાં કરતા ઓછી હોય છે.
(૪) રિંગ મોલ્ડનું દબાણ ઘટાડતું છિદ્ર ખૂબ મોટું છે, અને ખુલવાનો દર ખૂબ વધારે છે.
(5) કટીંગ બ્લેડની સ્થિતિ અને કોણ ગેરવાજબી છે.
(6) દાણાદાર તાપમાન.
(૭) રિંગ ડાઇ કટીંગ બ્લેડના પ્રકાર અને અસરકારક ઊંચાઈ (બ્લેડ પહોળાઈ, પહોળાઈ) પર અસર પડે છે.
(8) તે જ સમયે, કમ્પ્રેશન ચેમ્બરની અંદર કાચા માલનું વિતરણ અસમાન છે.
2. ફીડ અને ગોળીઓની ગુણવત્તાનું વિશ્લેષણ સામાન્ય રીતે તેમના આંતરિક અને બાહ્ય ગુણોના આધારે કરવામાં આવે છે. ઉત્પાદન પ્રણાલી તરીકે, આપણે ફીડ ગોળીઓની બાહ્ય ગુણવત્તા સંબંધિત બાબતો પ્રત્યે વધુ સંવેદનશીલ હોઈએ છીએ. ઉત્પાદનના દૃષ્ટિકોણથી, જળચર ફીડ ગોળીઓની ગુણવત્તાને અસર કરતા પરિબળોનો સારાંશ નીચે મુજબ આપી શકાય છે:
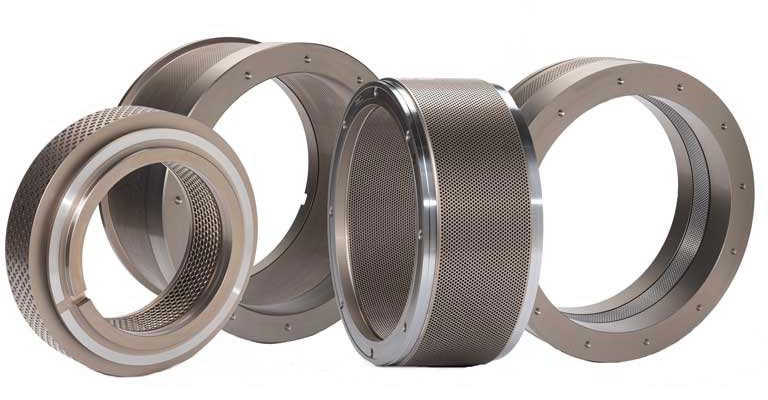
(૧) ફોર્મ્યુલાની ડિઝાઇન અને સંગઠનની સીધી અસર જળચર ફીડ ગોળીઓની ગુણવત્તા પર પડે છે, જે કુલ ગોળીઓના આશરે ૪૦% હિસ્સો ધરાવે છે;
(2) કચડી નાખવાની તીવ્રતા અને કણોના કદની એકરૂપતા;
(૩) રિંગ મોલ્ડનો વ્યાસ, સંકોચન ગુણોત્તર અને રેખીય વેગ કણોની લંબાઈ અને વ્યાસ પર અસર કરે છે;
(૪) રિંગ મોલ્ડનો કમ્પ્રેશન રેશિયો, રેખીય વેગ, ક્વેન્ચિંગ અને ટેમ્પરિંગ અસર, અને કટીંગ બ્લેડનો કણોની લંબાઈ પર પ્રભાવ;
(૫) કાચા માલની ભેજનું પ્રમાણ, ટેમ્પરિંગ અસર, ઠંડક અને સૂકવણીની અસર તૈયાર ઉત્પાદનોના ભેજનું પ્રમાણ અને દેખાવ પર પડે છે;
(6) સાધનો પોતે, પ્રક્રિયા પરિબળો, અને ક્વેન્ચિંગ અને ટેમ્પરિંગ અસરો કણ પાવડર સામગ્રી પર અસર કરે છે;
3. સંભાળવાના પગલાં:
(1) ફેબ્રિક સ્ક્રેપરની લંબાઈ, પહોળાઈ અને કોણ ગોઠવો, અને ઘસાઈ ગયેલા સ્ક્રેપરને બદલો.
(2) ઓછી ફીડિંગ રકમને કારણે ઉત્પાદનની શરૂઆતમાં અને અંતની નજીક કટીંગ બ્લેડની સ્થિતિને સમયસર ગોઠવવા પર ધ્યાન આપો.
(૩) ઉત્પાદન પ્રક્રિયા દરમિયાન, સ્થિર ખોરાક દર અને વરાળ પુરવઠો સુનિશ્ચિત કરો. જો વરાળનું દબાણ ઓછું હોય અને તાપમાન વધી ન શકે, તો તેને સમયસર ગોઠવવું જોઈએ અથવા બંધ કરવું જોઈએ.
(૪) વચ્ચેના અંતરને વ્યાજબી રીતે સમાયોજિત કરોરોલર શેલ. નવા રોલર્સ સાથે નવા મોલ્ડને અનુસરો, અને ઘસારાને કારણે પ્રેશર રોલર અને રિંગ મોલ્ડની અસમાન સપાટીને તાત્કાલિક રિપેર કરો.
(૫) રિંગ મોલ્ડના ગાઇડ હોલનું સમારકામ કરો અને બ્લોક થયેલા મોલ્ડ હોલને તાત્કાલિક સાફ કરો.
(6) રિંગ મોલ્ડનો ઓર્ડર આપતી વખતે, મૂળ રિંગ મોલ્ડની અક્ષીય દિશાના બંને છેડા પર છિદ્રોની ત્રણ હરોળનો સંકોચન ગુણોત્તર મધ્યમાં કરતા 1-2 મીમી નાનો હોઈ શકે છે.
(૭) શક્ય તેટલી તીક્ષ્ણ ધાર સુનિશ્ચિત કરવા માટે, ૦.૫-૧ મીમીની વચ્ચે નિયંત્રિત જાડાઈ સાથે નરમ કાપવાની છરીનો ઉપયોગ કરો, જેથી તે રિંગ મોલ્ડ અને પ્રેશર રોલર વચ્ચેની મેશિંગ લાઇન પર હોય.
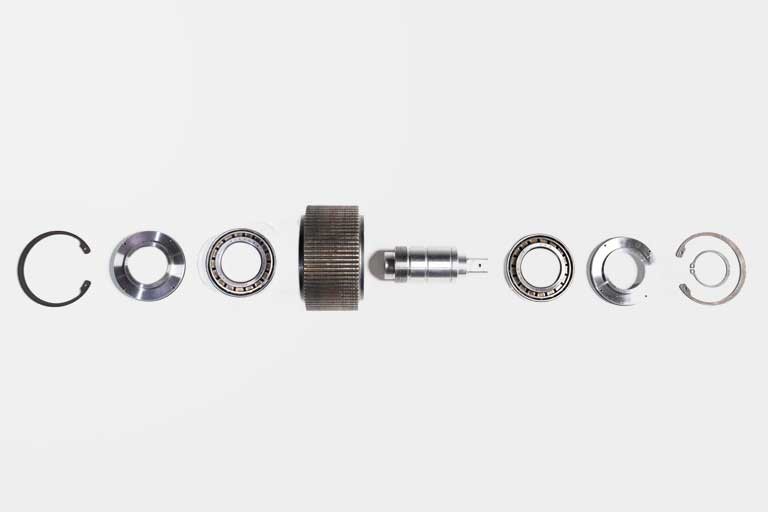
(8) રિંગ મોલ્ડની સાંદ્રતા સુનિશ્ચિત કરો, ગ્રાન્યુલેટરના સ્પિન્ડલ ક્લિયરન્સને નિયમિતપણે તપાસો અને જો જરૂરી હોય તો તેને સમાયોજિત કરો.
૬, સારાંશ નિયંત્રણ બિંદુઓ:
1. ગ્રાઇન્ડીંગ: ગ્રાઇન્ડીંગની સૂક્ષ્મતા સ્પષ્ટીકરણની આવશ્યકતાઓ અનુસાર નિયંત્રિત થવી જોઈએ.
2. મિશ્રણ: યોગ્ય મિશ્રણ જથ્થો, મિશ્રણ સમય, ભેજનું પ્રમાણ અને તાપમાન સુનિશ્ચિત કરવા માટે કાચા માલના મિશ્રણની એકરૂપતા નિયંત્રિત કરવી આવશ્યક છે.
૩. પરિપક્વતા: પફિંગ મશીનનું દબાણ, તાપમાન અને ભેજ નિયંત્રિત હોવા જોઈએ.
કણ સામગ્રીનું કદ અને આકાર: કમ્પ્રેશન મોલ્ડ અને કટીંગ બ્લેડના યોગ્ય સ્પષ્ટીકરણો પસંદ કરવા આવશ્યક છે.
5. તૈયાર ફીડમાં પાણીનું પ્રમાણ: સૂકવવાનો અને ઠંડુ કરવાનો સમય અને તાપમાન સુનિશ્ચિત કરવું જરૂરી છે.
૬. તેલ છંટકાવ: તેલ છંટકાવની ચોક્કસ માત્રા, નોઝલની સંખ્યા અને તેલની ગુણવત્તા પર નિયંત્રણ રાખવું જરૂરી છે.
7. સ્ક્રીનીંગ: સામગ્રીના સ્પષ્ટીકરણો અનુસાર ચાળણીનું કદ પસંદ કરો.
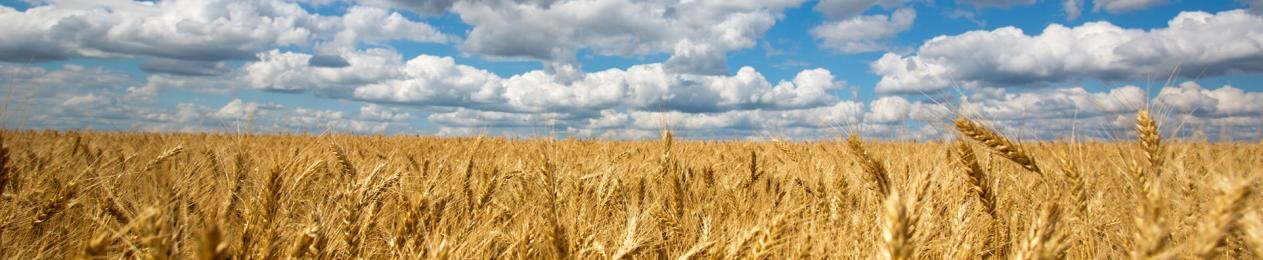
પોસ્ટ સમય: નવેમ્બર-૩૦-૨૦૨૩